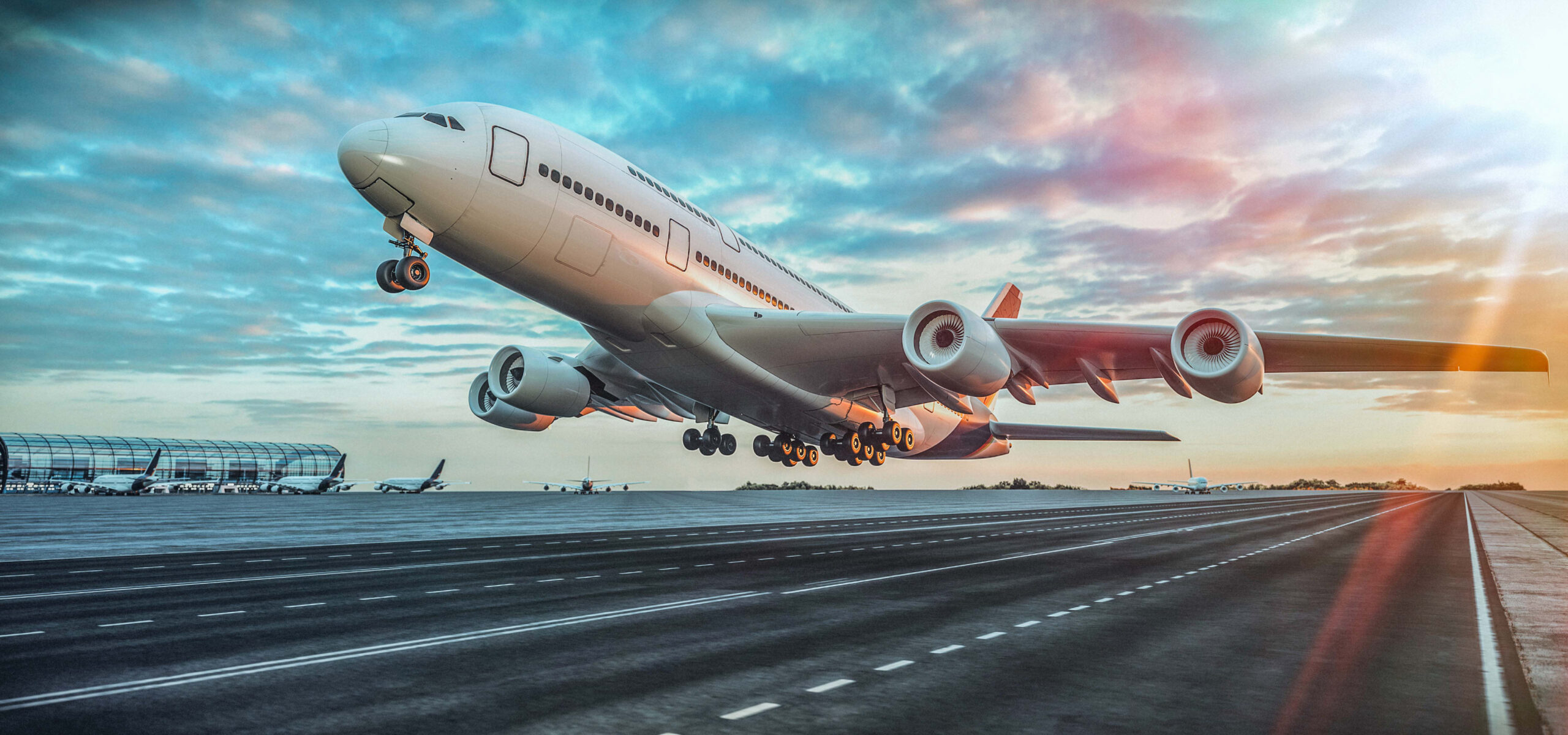
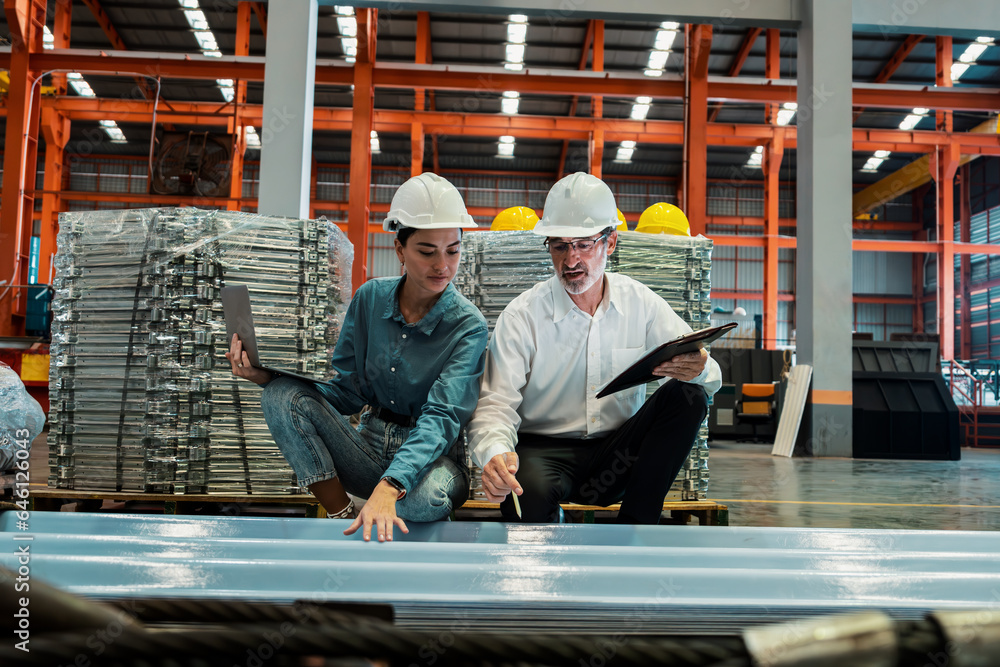
The process of creation has gotten us to where we are today. Without humankind constantly striving to improve, there would never have been a man on the moon or the ability to fly across the world in a day.
Composites are something that has been around in some shape or form for thousands of years. The Ancient Egyptians would form bricks using a variety of materials to improve their performance. This included the combination of mud and straw or clay, as well as wattle and daub, leading to an air-dried brick. As many of the pyramids are still standing, it appears that this approach has stood the test of time.
Composites generate surprising effects. The process of adding at least two different constituent materials together that have different chemical or physical properties can lead to an end product that has significantly enhanced characteristics than just the individual ingredients.
In the 1950s, composite materials were first being used in aircraft. This discovery led to the possibility of making aircraft significantly lighter, helping to reduce fuel costs. There was also the ability to create complex designs that still have strength in a particular direction that otherwise would not really be possible.
In the 20th century, M.C. Gill Corporation was mainly supplying raw materials during its initial years in business. However, it soon realized that there were ways it could add more value when it came to its products and services. This would lead to a competitive edge for the company and help turn it into a pioneer in composites manufacturing. It continually invested in its people and its equipment to make sure that it was constantly striving for more and not resting on its laurels.
As a result, the company transitioned from mainly being a manufacturer of raw materials to starting to construct composites in-house and providing customers with an end product that was effectively good to go. A large focus was different forms of flooring including for aircraft.
It was in 1990 that the company’s Northern Ireland facility saw a possible gap in the market. It started to consider offering its fabrication services to an important client. British Aerospace (BAe) was buying raw materials for its BAe Jetstream 41 (J41) and BAe Jetstream 31 (J31) at the time. This relationship paved the way for the development of the cut and fold technique.
There are a lot of different ways in which composite materials are utilized in the aviation sector. These types of materials have plenty of uses, helping to minimize the weight of an aircraft, as well as having great flexibility in terms of its applications.
One of the most popular techniques that have come to the fore in recent years in the aviation sector with the use of composite materials is the cut and fold technique. This process sees slots being cut across a honeycomb core sandwich panel. The panel will then be folded in order to make a non-linear shape.
The bigger the slot, the greater the angle created through the fold will be. Through the cutting of multiple slots, the fabricator is able to get a radiused fold that is not going to be a possibility if using any other types of techniques. As soon as it has been folded, a number of different adhesives can then be utilized to bond the materials so the shape remains the same.
M.C. Gill Europe has been using this cut and fold technique for some time as opposed to methods that are more expensive and would require a lot of equipment and tools in the creation of 3D composite shapes.
After the success that M.C. Gill Europe saw through its collaboration with BAe, it came to an agreement with AirBus in order to design and develop a flooring system that was both extremely lightweight and robust for the cockpit/fuselage area in the A380. The specific product that was deemed to be the ideal fit for this project was the Gillfab 5509.
This is a low-smoke panel for aircraft that has its facings created by phenolic resin that has been reinforced using Kevlar honeycomb core and cross-plied unidirectional carbon. This end product is very light in weight and a thin layer of fiberglass on the facings helps to prevent galvanic corrosion. The resulting design of the flooring led to the reduction of the budgeted weight of the entire package by 24%.
Naturally, M.C. Gill Europe utilized the cut and fold technique once more when it came to the predominant electric equipment area in the complex support structures that were multi-level. These areas would need regular maintenance access in what is limited space. The main concern was the weight, shape, and durability.
Therefore, M.C. Gill Europe makes specific solutions that are tailored towards each of these concerns. This included reinforcing individual parts through the folding of edges to create a knuckle and folding extended panels in order to make integral supports/legs so no extra metal structures were necessary.
This project turned out to be a success and led to further significant projects down the line that incorporated the cut and fold technique.
After the successful implementation of the cut and fold technique by M.C. Gill Europe with the A380, it began to look at other potential opportunities in the space that it could pursue.
In 2010, M.C. Gill Corporation struck a deal with Israel Aerospace Industries (IAI) for their Gulfstream G280 executive jet program. The IAI had a goal of getting the M.C. Gill designers to create a way in which the ceiling and side walls could be fitted out in the walk-in baggage area to have a certain type of finish.
What was different this time around with the cut and fold techniques was that the parts were not going to be used for structural, functional, or hidden parts (or ones that would be finished with paint). With the G280, each of the parts was going to be completely viewable by both the operators and owners of the aircraft.
The obstacle was that the hiding of cut lines on the faces that were visible would restrict the design of the part relating to its external closed folds. Eventually, the M.C. Gill Europe technical manager and IAI designers managed to develop a new technique whereby the finished parts could be made having both convex and concave folds. This ultimately proved to be a success in both functional and aesthetic senses.
M.C. Gill Europe was showcasing that its cut and fold technique was leading to lower tooling costs, as well as no longer needing the use of autoclave or oven equipment. All that was needed were simple jigs. Therefore, the technique is very flexible and can be customized and modified as necessity dictates. As a result of this project, M.C. Gill Europe could begin to offer complete design solutions.
There is clearly a massive use case for composite materials in the aviation sector. They can help to reduce weight by a significant amount, leading to lower fuel costs. More and more different forms of aircraft are now implementing composite materials in certain parts of the design and development process.
Composite materials are also known for being able to withstand moisture damage, as well as chemical erosion from acid rain and the likes. This leads to lower maintenance and replacement costs over time. One of the big advantages is the ability for these materials to mold into most types of shapes without the need for using high-pressure tools. The resulting shapes will also be able to have strength in whichever direction you choose.
Also, composite materials are not good conductors of heat or electricity, so it is a great way for you to insulate important parts on an aircraft. If you need some conductivity, composite materials can merge with certain parts that are thermally conductive as needed.
There are numerous different ways in which these composite materials are formed and techniques used to enhance the end result. In recent years, the cut and fold technique has become very popular. It is now a key part of numerous notable aircraft. Over time, the likes of M.C. Gill Europe will continue investing in research and development in an attempt to try to improve the applications even further.